
Inadequate Internal Resources for EHS Management: A Hidden Risk to Organizational Success
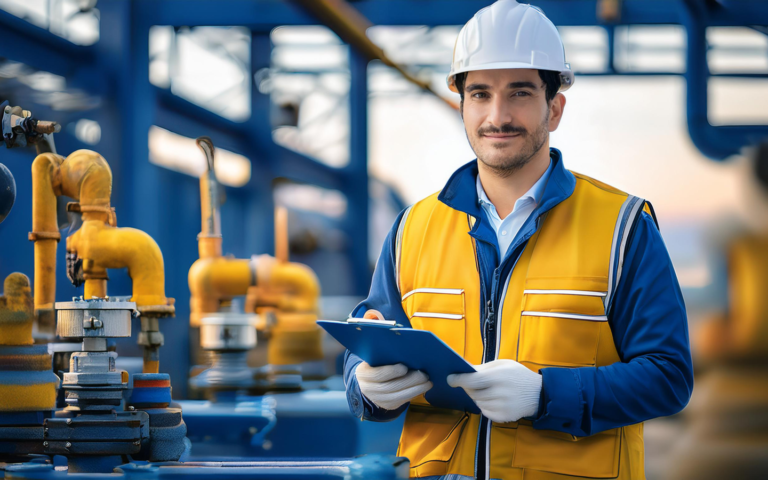
Environmental, Health, and Safety (EHS) management is essential for protecting employees, ensuring regulatory compliance, and maintaining operational efficiency. However, many organizations face challenges due to inadequate internal resources allocated for EHS management. This lack often results in increased workplace incidents, regulatory violations, and financial penalties. A strategic approach to addressing these deficiencies can protect businesses from these risks while enhancing productivity and compliance.
The Consequences of Inadequate Resources
Organizations with limited EHS resources frequently struggle to meet regulatory requirements, maintain workplace safety, and prepare for emergencies. These challenges include:
- Regulatory Non-Compliance: Failing to meet OSHA, EPA, and DOT standards increases the risk of fines and operational shutdowns.
- Higher Incident Rates: Underfunded EHS programs often result in workplace injuries, illnesses, and near misses. According to OSHA, companies with insufficient EHS management report injury rates 30% higher than organizations with robust systems (Workplace Injury, Illness and Fatality Statistics, 2023).
- Reduced Employee Engagement: Employees are less likely to feel safe or motivated in workplaces lacking clear safety protocols and adequate training.
- Operational Disruptions: Delayed responses to incidents or hazards can lead to costly downtime and reputational damage.
The lack of internal resources for EHS management is not just a compliance issue—it’s a business risk that impacts operational sustainability.
Industry-Specific Challenges
Transportation Industry
Transportation companies face unique risks, such as vehicle accidents, hazardous materials spills, and logistical disruptions. Inadequate EHS resources can result in non-compliance with DOT and FRA standards, increasing the likelihood of accidents and public safety risks.
Construction Industry
With inherently hazardous worksites, construction companies need constant oversight to prevent falls, equipment failures, and structural collapses. Without sufficient EHS resources, they risk non-compliance with OSHA’s construction standards (Safety and Health Regulation for Construction, 2024), leading to higher injury rates and project delays.
General Industry
Across general industries, inadequate EHS resources often result in compliance gaps with OSHA’s general industry standards (Occupational Safety and Health Standards, 2024), leading to increased injuries, reduced productivity, and financial losses.
Environmental Industry
Environmental organizations face strict EPA regulations to prevent pollution and ensure sustainability. A lack of dedicated EHS resources can result in spills, emissions violations, and reputational damage that impact both the environment and public trust.(EPA, Compliance, 2024)
Building a Comprehensive EHS Program
Addressing the resource gap requires a strategic approach, including:
- Conducting Resource Assessments: Evaluating current EHS capabilities and identifying gaps in staffing, training, and technology.
- Leveraging Technology: Implementing compliance management software to streamline reporting, monitoring, and auditing processes.
- Employee Training: Regularly educating employees on safety protocols, hazard identification, and emergency response.
- Establishing Key Performance Indicators (KPIs): Tracking and analyzing safety metrics to monitor progress and make data-driven decisions.
- Outsourcing Expertise: Partnering with EHS consultants to provide on-demand support and ensure compliance with evolving regulations.
By implementing these strategies, organizations can create a safer, more efficient workplace and reduce risks associated with resource deficiencies.
Relation to the Four Key Areas of Safety
Inadequate internal resources for EHS management affect all four critical areas of safety:
- Employee Safety: Employees face increased hazards and lack the tools to protect themselves effectively.
- Process Safety: Critical operations are more prone to failures, leading to costly incidents.
- Environmental Safety: Insufficient oversight can result in environmental harm and regulatory violations.
- Public Safety: Communities surrounding industrial operations are at greater risk from accidents or hazardous materials.
Addressing these gaps ensures a holistic approach to safety management and builds trust with stakeholders.
Key Safety Practices for Effective EHS Management
Organizations striving to overcome resource deficiencies should adopt the following practices:
- Regular Training and Certifications: Keeping employees informed and skilled in identifying and addressing workplace hazards.
- Frequent Safety Audits: Regularly inspecting facilities to identify and rectify safety concerns.
- Incident Reporting and Analysis: Thoroughly investigating incidents to implement preventive measures.
- Emergency Preparedness: Developing and practicing response plans for potential crises.
- Open Communication: Encouraging employees to report safety concerns without fear of retaliation.
- Dedicated Safety Leadership: Appointing experienced EHS professionals to lead safety initiatives.
- Leveraging External Support: Partnering with EHS consultants to provide expert guidance and fill resource gaps.
- Compliance Monitoring: Using tools and checklists to ensure adherence to OSHA, EPA, DOT, and other standards.
- Proactive Risk Assessments: Anticipating potential hazards and mitigating risks before they escalate.
- Continuous Improvement: Regularly updating protocols and strategies based on feedback and evolving regulations.
How Key Safety LLC Can Help
At Key Safety LLC, we understand the challenges posed by inadequate internal EHS resources. Our tailored solutions include:
- Document Development for Start-up Projects: Comprehensive manuals, SOPs, and policies to establish a foundation for safety and compliance.
- Service on Demand: Immediate support for safety audits, compliance checks, and incident investigations.
- Regular Consultation Services: Ongoing EHS support through site visits, employee training, and compliance management.
Our expertise helps businesses fill critical resource gaps, ensuring safety, compliance, and operational excellence.
Conclusion
Inadequate internal resources for EHS management present significant risks to businesses across all industries. However, these challenges can be addressed with a proactive approach, leveraging technology, training, and expert support. By partnering with Key Safety LLC, organizations can overcome resource deficiencies, enhance safety, and achieve sustainable growth.
Ready to strengthen your EHS program? Schedule a free consultation today and visit our blog for more insights.
References
Occupational Safety and Health Administration. (2023). OSHA Statistics on Workplace Injuries and Illnesses. https://www.osha.gov/data/work
Standards for Safety and Health Regulations for Construction, OSHA 29 CFR 1926 (2024). https://www.osha.gov/laws-regs/regulations/standardnumber/1926
Standards for Occupational Safety and Health Standards, OSHA 29 CFR 1910 (2024). https://www.osha.gov/laws-regs/regulations/standardnumber/1910
Environmental Protection Agency. (2024). EPA Compliance Assistance. https://www.epa.gov/compliance
Federal Railroad Administration. (2019). System Safety Program Overview. https://railroads.dot.gov/rail-network-development/passenger-rail/system-safety-program