
Navigating Complex Regulatory Landscapes: A Strategic Advantage in Safety Management
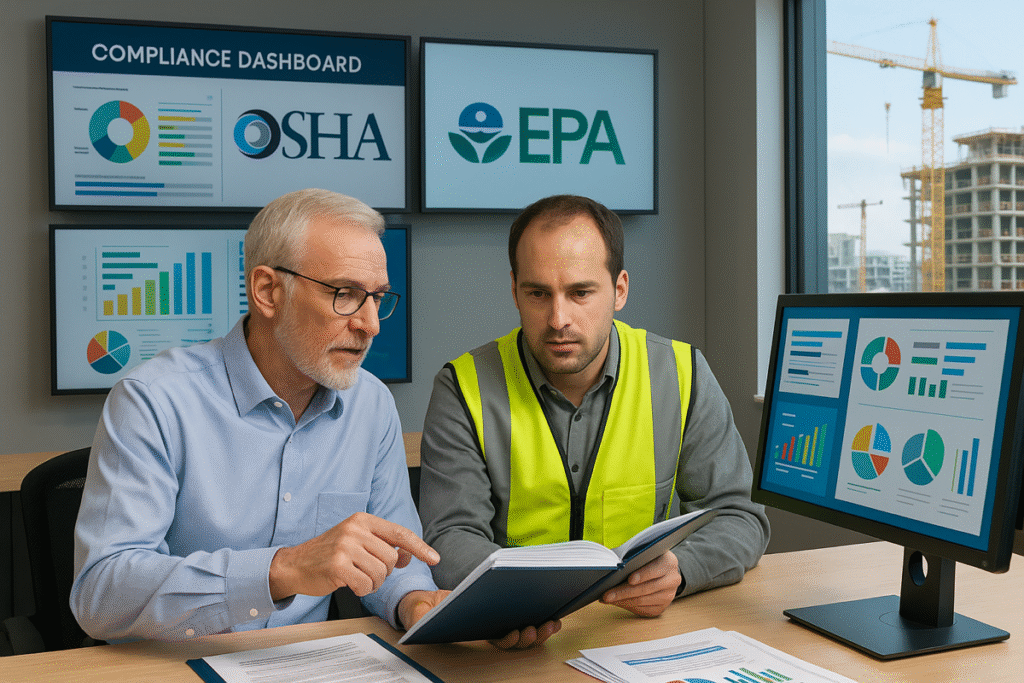
In today’s business environment, companies across industries face increasing pressure to comply with a growing web of safety, environmental, and operational regulations. From OSHA’s evolving standards to the integration of ISO frameworks and local environmental laws, the regulatory landscape has become not only more complex but also more unforgiving. For professionals in construction, manufacturing, transportation, and railroads, the ability to understand and anticipate these regulations is not just a compliance requirement it’s a strategic necessity.
Failing to comply is no longer just about fines or citations. It affects brand credibility, employee morale, and client trust. Navigating this complexity requires more than internal policies it demands a proactive, knowledgeable, and adaptable approach. That’s why companies are increasingly partnering with safety consultants who specialize in making sense of regulatory overlap and operational demands.
Complex regulatory environments are not static they evolve rapidly, particularly in response to industrial incidents, environmental pressures, and legal precedents. For example, OSHA regularly updates its standards to reflect emerging risks and technologies. Its focus has expanded to include not only traditional hazards but also psychosocial factors, fatigue, and climate-adaptive policies like emergency preparedness in hurricane-prone zones (Emergency Preparedness and Response, 2024). This dynamic nature means that businesses must maintain an ongoing process of compliance evaluation, not a one-time checklist.
In the construction sector, navigating regulations means reconciling federal OSHA guidelines with state-specific amendments and local ordinances. Miami-Dade County, for instance, enforces strict permitting and environmental review procedures that go beyond standard OSHA requirements. Projects that neglect these layers may face legal hold-ups, financial penalties, or reputational damage. Similarly, the manufacturing sector must respond not only to OSHA but also to EPA emission standards, FDA protocols for consumables, and the Department of Transportation’s safety controls for handling and transporting hazardous materials (Laws & Regulations, 2024).
For companies managing multi-state operations or national contracts, regulatory complexity multiplies. Transportation companies operating across state lines must account for the Federal Motor Carrier Safety Administration (FMCSA) rules, differing state DOT interpretations, and industry-specific mandates like Electronic Logging Devices (ELDs) and Hours of Service (HOS) compliance (Regulations, 2024). A missed update in one region can trigger cascading operational setbacks across others.
The challenge deepens when industries intersect. Consider railroad-adjacent construction zones. These projects must comply with Occupational Safety and Health Administration (OSHA), Federal Railroad Administration (FRA), and local transit authorities each with unique documentation, inspection, and worker certification requirements. In such high-risk interfaces, clarity and consistency in regulatory understanding become not just useful but essential.
One of the most overlooked challenges in compliance is documentation. Companies often struggle with fragmented reporting, outdated SOPs, or inconsistent inspection protocols. This creates vulnerabilities during audits and reduces internal confidence in safety practices. Many organizations fail not because of a lack of intent but because of a lack of integration between departments. Safety teams, HR, field supervisors, and compliance officers may each operate on different understandings of regulatory expectations. This misalignment can lead to duplicated efforts or critical omissions both costly errors in regulated environments.
The solution is not more documentation it’s smarter documentation. Regulatory frameworks such as ISO 45001 and ISO 14001 emphasize risk-based thinking and integration into business processes (Occupational health and safety management systems, 2024). By aligning documentation systems with these principles, companies can better anticipate compliance needs, delegate responsibilities appropriately, and respond to regulatory shifts efficiently.
Another crucial aspect of navigating complex regulations is workforce education. Training programs should not merely meet the minimum standard; they should create real-world understanding of why regulations exist and how they protect both people and operations. Certifications, refreshers, and scenario-based learning not only reduce the risk of non-compliance but also increase employee engagement in safety culture. A workforce that understands the “why” behind a regulation is far more likely to follow it consistently, even under operational stress.
Leadership plays a pivotal role in regulatory navigation. Executives must stop viewing compliance as a cost center and start seeing it as a value proposition. In a world where clients and investors are scrutinizing ESG (Environmental, Social, Governance) practices, regulatory compliance is now a reflection of corporate integrity and foresight. Businesses that can demonstrate clear, organized, and ethical regulatory practices attract better partnerships, reduce insurance liabilities, and mitigate long-term operational risks.
This is where external EHS consulting adds measurable value. Firms like Key Safety LLC bring industry-specific knowledge, updated regulatory frameworks, and proven systems for streamlining compliance. Rather than relying on internal teams to “figure it out” after a violation or a failed audit, businesses benefit from foresight, structured implementation, and scalable training programs. A consultant doesn’t just interpret the rules they help integrate them into daily operations, aligning them with business goals and field realities.
For growing companies, this regulatory navigation must begin early. Start-ups and expanding operations need to embed safety into their workflows from day one. Doing so avoids retrofitting compliance and establishes a culture of accountability that scales. The longer a company waits to address regulatory complexity, the more expensive and disruptive compliance becomes later.
In 2025, companies that want to thrive not just survive must treat regulatory complexity as a leadership priority. That means investing in systems that turn compliance into a core capability. It means embracing transparency, training, and external expertise. And it means selecting partners who understand that real-world operations rarely fit neatly into theoretical frameworks and who know how to bridge the gap.
Key Safety LLC understands the pressures professionals face in high-risk industries. Our mission is not just to interpret regulations, but to empower teams to implement them effectively, safely, and strategically. Navigating complex regulatory landscapes isn’t a burden when you have the right guide. It’s a competitive advantage.
References
Environmental Protection Agency. (2024). Laws & regulations. https://www.epa.gov/laws-regulations
Federal Motor Carrier Safety Administration. (2024). Regulations. https://www.fmcsa.dot.gov/regulations
International Organization for Standardization. (2023). ISO 45001 – Occupational health and safety. https://www.iso.org/iso-45001-occupational-health-and-safety.html
Occupational Safety and Health Administration. (2024). Emergency preparedness and response. https://www.osha.gov/emergency-preparedness
Comments: