
Lifting Safety Across Industries
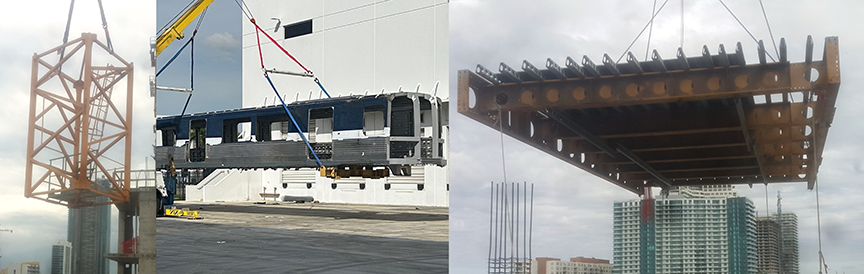
Lifting safety is a critical component of workplace health and safety across all industries. From construction sites to general industry settings and railroads, proper lifting practices can prevent serious injuries. The Occupational Safety and Health Administration (OSHA), along with standards from the American National Standards Institute (ANSI), Department of Transportation (DOT), and Federal Railroad Administration (FRA), provides specific guidelines for lifting safely in different environments. This journal examines why lifting safety is crucial and explores best practices that can reduce injury risks.
The Importance of Lifting Safety
Lifting tasks are routine in many workplaces, yet they present significant risks when performed improperly. Back injuries caused by lifting can lead to long-term disability, and in severe cases, these injuries are permanent. OSHA has established specific standards for lifting safety across various industries, such as 29 CFR 1926.21 for construction and 29 CFR 1910.176 for general industry, ensuring that employers provide the necessary training and equipment. Following these guidelines not only prevents injuries but also reduces costs associated with workplace incidents.
Lifting Safety in Construction
The construction industry frequently involves lifting heavy and awkward loads, which poses unique risks. According to OSHA 29 CFR 1926.21, workers must be trained in recognizing hazards associated with lifting and handling materials. This includes ensuring proper body mechanics, using mechanical aids when necessary, and working in teams to lift heavy loads. Given the dynamic nature of construction sites, workers must also be aware of environmental factors like uneven surfaces and weather conditions that can affect lifting safety.
Lifting Safety in General Industry
In general industry, lifting tasks are governed by OSHA standard 29 CFR 1910.176. Improper lifting techniques often lead to musculoskeletal injuries, which can be prevented with proper training and ergonomic tools. The standard requires that employers ensure employees are trained in safe lifting techniques, proper load handling, and the use of mechanical aids. Additionally, regular inspections of lifting equipment and clear communication about safety protocols are essential to maintain a safe work environment.
Lifting Safety in the Railroad Industry
The railroad industry presents unique challenges in lifting safety due to the need to handle equipment and materials in confined spaces and on moving platforms. FRA regulations, such as 49 CFR 213.353, outline the requirements for safe material handling and lifting operations. These standards emphasize the importance of securing loads, using specialized lifting devices, and ensuring that workers are trained to recognize and mitigate lifting hazards unique to the rail environment.
Integrating Lifting Safety into the Four Key Areas of Safety
Lifting safety is integral to the four key areas of workplace safety: hazard identification, risk assessment, incident prevention, and emergency preparedness. When lifting tasks are rushed, the likelihood of misjudging hazards or skipping essential safety steps increases, leading to higher risks of injury. Organizations must integrate lifting safety into their overall safety programs, ensuring that workers are aware of potential hazards and equipped with the knowledge and tools needed to lift safely.
Common Safety Practices for Lifting Safety
To mitigate risks associated with lifting, employers should implement the following practices:
- Proper Training: Provide comprehensive training on lifting techniques, including body mechanics and the use of mechanical aids.
- Load Assessment: Always assess the load before lifting, considering its weight, size, and stability.
- Use Mechanical Aids: Utilize equipment such as hoists, cranes, or dollies when available to reduce strain on workers.
- Team Lifting: For heavy or bulky items, use a team-lifting approach to distribute the weight evenly.
- Clear Pathways: Ensure that the path is clear of obstacles and that the surface is stable before lifting.
- Proper Body Mechanics: Encourage workers to lift with their legs, not their back, and to avoid twisting while lifting.
- Wear Appropriate PPE: Gloves, safety boots, and back supports can offer additional protection.
- Communication: Maintain open communication about the task and any potential hazards that may arise.
- Regular Equipment Inspections: Routinely inspect lifting equipment and tools for damage or wear.
- Foster a Safety Culture: Promote a culture where safety is prioritized over speed, ensuring all safety protocols are consistently followed.
Conclusion
Lifting safety is not merely about compliance with regulations; it is about protecting workers from potentially life-changing injuries. By understanding the risks and implementing best practices, employers can create a safer work environment. Emphasizing training, proper equipment use, and a strong safety culture will significantly reduce lifting-related incidents, making workplaces safer for all.
References
Standard for Safety Training and Education. OSHA 29 CFR § 1926.21 (2015).
https://www.osha.gov/laws-regs/regulations/standardnumber/1926/1926.21
Standard for Handling Materials – General. OSHA 29 CFR § 1910.176 (2015).
https://www.osha.gov/laws-regs/regulations/standardnumber/1910/1910.176
Standard for Turnouts, Crossovers, and Lift Rail Assemblies or Other Transition Devices
on Moveable Bridges. FRA 49 CFR § 213.353. Subpart G (2024).
https://www.ecfr.gov/current/title-49/subtitle-B/chapter-II/part-213/subpart-G/section-213.353