
Risk Management in Construction, General Industry, and Railroad Industry
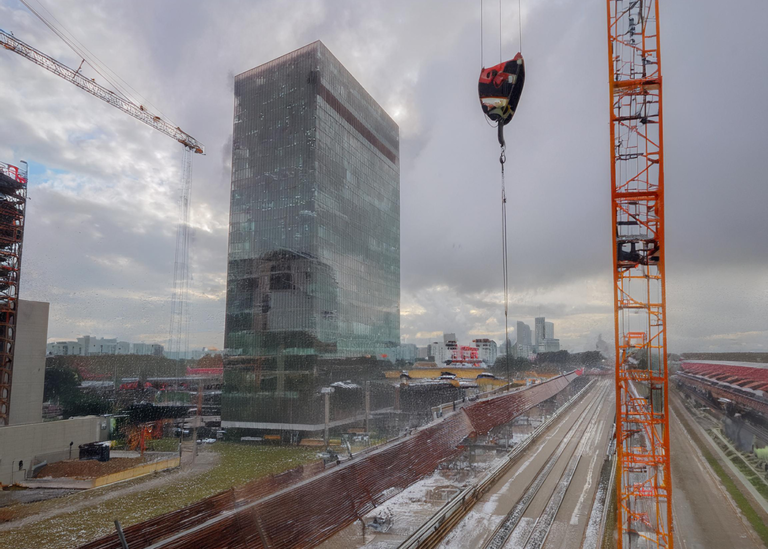
Risk management is a vital process across construction, general industry, and railroad sectors. By identifying, assessing, and controlling potential hazards, organizations can prevent accidents, comply with regulations, and ensure the well-being of employees and the public. This journal explores the importance of risk management, supported by national statistics, and offers best practices to enhance safety performance in various industries.
Introduction
Risk management involves systematic processes aimed at identifying, assessing, and mitigating risks to ensure safety and compliance. Across industries, this practice is crucial for minimizing incidents, improving operational efficiency, and fostering a culture of safety. According to the National Safety Council (NSC), workplaces with robust risk management programs report a 48% reduction in injury rates (National Safety Council, 2022).
The Importance of Risk Management Across Industries
Risk Management in Construction
The construction industry is inherently hazardous due to activities like working at heights, operating heavy machinery, and handling hazardous materials. OSHA’s standard 29 CFR 1926 focuses on construction safety, including fall protection (Duty to Have Fall Protection, 2017) and excavation safety (Excavations, 2022). Implementing risk management practices in construction can significantly reduce accidents and fatalities, promoting a safer work environment.
Risk Management in General Industry
In general industry, risk management covers a wide range of activities, from machine operation to chemical handling. OSHA’s standard 29 CFR 1910 addresses general industry safety, detailing requirements for machine guarding (Machine Guarding, 2021) and hazardous waste operations (Hazardous Waste Operations and Emergency Response, 1990). Proper risk management ensures compliance and minimizes incidents, leading to safer workplaces and increased productivity.
Risk Management in the Railroad Industry
The railroad industry faces unique risks, including train operations, track maintenance, and hazardous material transport. The Federal Railroad Administration (FRA) sets standards for risk management, including track safety (Track Safety Standards, 2020) and safety training (Training, Qualification, and Oversight for Safety-Related Railroad Employees, 2014). Effective risk management in this sector is essential for preventing accidents, ensuring passenger safety, and safeguarding the environment.
Information and the Four Key Areas of Safety
Risk management is integral to the four key areas of safety: policy, risk management itself, safety promotion, and safety assurance. Accurate information allows organizations to identify hazards, assess risks, implement controls, and continuously monitor safety performance. This data-driven approach ensures that safety policies are effective, risks are managed proactively, and a culture of safety is promoted.
Best Practices for Risk Management in the USA
- Risk Assessment and Analysis: Conduct regular risk assessments to identify potential hazards and evaluate their impact. Use tools like Job Safety Analysis (JSA) and Hazard and Operability Study (HAZOP) for detailed evaluations.
- Safety Training and Awareness: Provide comprehensive training on safety protocols and emergency procedures to all employees. This includes OSHA’s HAZWOPER training for hazardous waste operations (Hazardous Waste Operations and Emergency Response, 1990).
- Use of Personal Protective Equipment (PPE): Ensure the proper use of PPE, such as helmets, gloves, and fall arrest systems, particularly in high-risk industries like construction (Personal Protective Equipment, 2024).
- Regular Safety Audits and Inspections: Conduct frequent safety audits to identify unsafe conditions and ensure compliance with regulations like OSHA’s General Safety and Health Provisions.
- Emergency Preparedness and Response: Develop and implement emergency action plans to address potential incidents, as outlined in OSHA’s (Emergency Action Plans, 2017).
- Safe Work Procedures: Establish standard operating procedures (SOPs) for hazardous tasks, ensuring they align with industry best practices and regulatory requirements.
- Incident Reporting and Analysis: Implement a system for reporting and analyzing incidents and near-misses to identify root causes and prevent recurrence.
- Safety Culture and Employee Involvement: Promote a safety culture by involving employees in risk management processes and encouraging the reporting of hazards.
- Continuous Improvement: Regularly review and update risk management practices to adapt to changing work environments and emerging risks.
- Compliance with Regulations: Stay up-to-date with OSHA, FRA, EPA, and ISO regulations to ensure compliance and integrate these standards into your risk management program.
Conclusion
Risk management is a fundamental aspect of workplace safety across construction, general industry, and railroad sectors. By implementing risk management practices, organizations can prevent accidents, comply with regulatory standards, and promote a culture of safety. Utilizing a systematic approach to risk identification, assessment, and mitigation not only safeguards workers but also enhances operational efficiency and productivity.
References
National Safety Council. (2022). Workplace Injury Facts. https://www.nsc.org/
Standard for Duty to Have Fall Protection. OSHA 29 CFR § 1926.501 Subpart M (2017). https://www.osha.gov/laws-regs/regulations/standardnumber/1926/1926.501
Standard for Excavations. OSHA 29 CFR § 1926.651 Subpart P (2022). https://www.osha.gov/laws-regs/regulations/standardnumber/1926/1926.651
Standard for General Requirements for all Machines. OSHA 29 CFR § 1910.212 Subpart O (2021). https://www.osha.gov/laws-regs/regulations/standardnumber/1910/1910.212
Standard for Hazardous Waste Operations and Emergency Response. OSHA 29 CFR 1910.120 Subpart H (1990). https://www.osha.gov/laws-regs/regulations/standardnumber/1910/1910.120
Standard for Personal Protective Equipment. OSHA 29 CFR § 1926.28 Subpart C (2024). https://www.osha.gov/laws-regs/regulations/standardnumber/1926/1926.28
Standard for Emergency Action Plans. OSHA 29 CFR § 1910.38 Subpart E (2017). https://www.osha.gov/laws-regs/regulations/standardnumber/1910/1910.38
Standard for Track Safety Standards. FRA 49 CFR Part 213 (2020). https://www.ecfr.gov/current/title-49/subtitle-B/chapter-II/part-213
Standard for Training, Qualification, and Oversight for Safety-Related Railroad Employees. FRA 49 CFR Part 243 (2014). https://www.ecfr.gov/current/title-49/part-243
ISO. (2018). ISO 45001:2018 Occupational Health and Safety Management Systems.https://www.iso.org/standard/63787.html