
How Operational Disruptions Drain Your Finances and How to Prevent Them
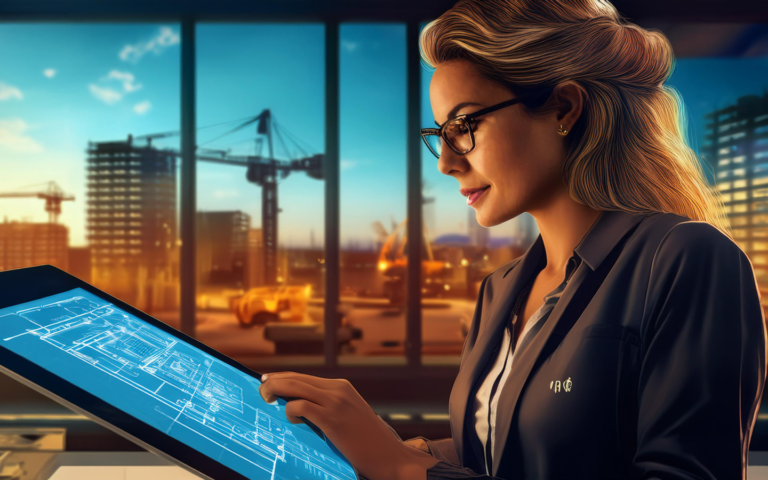
Every business faces challenges, but operational disruptions can be the most costly and damaging. Whether due to supply chain failures, safety incidents, equipment breakdowns, or compliance violations, disruptions can lead to massive financial losses, lost productivity, and reputational damage.
From construction delays to manufacturing shutdowns and railroad service interruptions, unplanned disruptions impact every industry. Understanding their financial impact and taking preventive measures can save businesses millions in lost revenue and penalties.
This guide explores:
✅ The hidden financial costs of operational disruptions.
✅ How businesses can mitigate financial risks through preventive strategies.
✅ Why integrating risk management and EHS (Environmental, Health, and Safety) practices prevents disruptions.
✅ How Key Safety LLC can help businesses reduce financial exposure.
The Hidden Financial Costs of Operational Disruptions
When a business experiences unplanned disruptions, the financial consequences extend beyond just immediate losses. Here’s what companies often face:
1. Lost Revenue and Productivity
🚨 Every minute of downtime costs money.
- Manufacturing plants lose an average of $260,000 per hour due to production stoppages.
- Construction project delays lead to contract penalties, increased labor costs, and material waste.
- Railroad service disruptions result in supply chain bottlenecks and customer dissatisfaction.
2. Increased Insurance Premiums and Legal Fees
🚨 Safety violations and workplace accidents lead to:
✔️ Higher workers’ compensation claims.
✔️ Expensive lawsuits from injured workers or clients.
✔️ Increased insurance premiums, raising operational costs.
3. Compliance Fines and Penalties
🚨 Failure to meet OSHA, EPA, and industry-specific safety regulations can result in:
- OSHA fines up to $15,625 per violation.
- Legal action from government agencies and affected employees.
- Reputational damage, leading to lost contracts and clients.
4. Equipment Downtime and Repair Costs
🚨 Unplanned machinery failures impact productivity and incur emergency repair expenses.
- Unmaintained heavy machinery leads to costly repairs and replacements.
- Unexpected failures cause supply chain interruptions, delaying deliveries and increasing costs.
🔹 Did You Know?
📌 75% of businesses have experienced major financial losses due to operational disruptions.
📌 Unplanned downtime accounts for $50 billion in annual losses across U.S. industries.
📌 Companies with proactive risk management save up to 40% on operational costs.
How to Minimize Financial Losses from Operational Disruptions
To protect your company’s bottom line, businesses must adopt preventive measures that reduce downtime, improve compliance, and enhance workplace safety.
✅ 1. Implement a Risk Management Plan
✔️ Conduct regular risk assessments to identify potential disruptions.
✔️ Create contingency plans for equipment failures, supply chain issues, and safety incidents.
✔️ Develop emergency response protocols to minimize downtime impact.
✅ 2. Invest in Preventive Maintenance
✔️ Schedule regular equipment inspections and maintenance to avoid costly failures.
✔️ Use IoT-based monitoring systems to detect machinery wear and tear.
✔️ Train employees on proper equipment handling and troubleshooting.
✅ 3. Strengthen Compliance to Avoid Fines and Shutdowns
✔️ Conduct internal safety audits to ensure OSHA, EPA, and FRA (Federal Railroad Administration) compliance.
✔️ Provide ongoing employee training on workplace safety and risk management.
✔️ Maintain detailed safety documentation to reduce legal liabilities.
✅ 4. Leverage Automation and AI for Operational Stability
✔️ Use automated compliance tracking to stay ahead of regulatory changes.
✔️ Implement AI-driven predictive analytics to forecast potential disruptions.
✔️ Digitize incident reporting systems to enhance response times.
✅ 5. Partner with Industry Experts for Risk Mitigation
✔️ Work with EHS and risk management consultants to identify operational vulnerabilities.
✔️ Create a business continuity plan with expert guidance.
✔️ Key Safety LLC provides customized safety and compliance solutions to prevent financial losses.
How Key Safety LLC Helps Businesses Reduce Financial Exposure
At Key Safety LLC, we provide:
✔️ Proactive risk assessment to prevent costly disruptions.
✔️ Custom compliance solutions to avoid OSHA violations and penalties.
✔️ Incident response planning to minimize downtime and financial loss.
✔️ Workplace safety training to reduce injuries and legal risks.
📞 Concerned about financial losses due to disruptions? Contact Key Safety LLC today to implement a cost-saving risk management strategy!
Conclusion
Operational disruptions are more than just temporary setbacks—they cost businesses millions in lost revenue, compliance fines, and legal liabilities. By implementing preventive measures and working with risk management experts, companies can protect their financial stability while ensuring safe and efficient operations.
🚀 Safeguard your business today. Contact Key Safety LLC to prevent financial losses from operational disruptions!